Configuration Case Study: Tesla
A quick story about Tesla's ECU Vertical
Toyota and Volkswagen are giants. Maybe not in terms of growth rate and innovation, but certainly in terms of scale. I suspect in a few years when Toyota's solid state batteries are fully deployed, we’ll be changing our tune, but at least up until today, Tesla's configuration in technology set it apart.
The recent teardown of the Model 3 by Nikkei Business Publications highlighted Tesla's advanced integrated central control unit. The integration is a significant distinction from the rest of the market.
Also known as Hardware 3, this little piece of tech is the company's biggest weapon in the burgeoning EV market. It could end the auto industry supply chain as we know it.
An engineer from one of the big Japanese manufacturers looked at it and said, "We cannot do it," and estimated that it would take six years for their firm to catch up to Tesla.
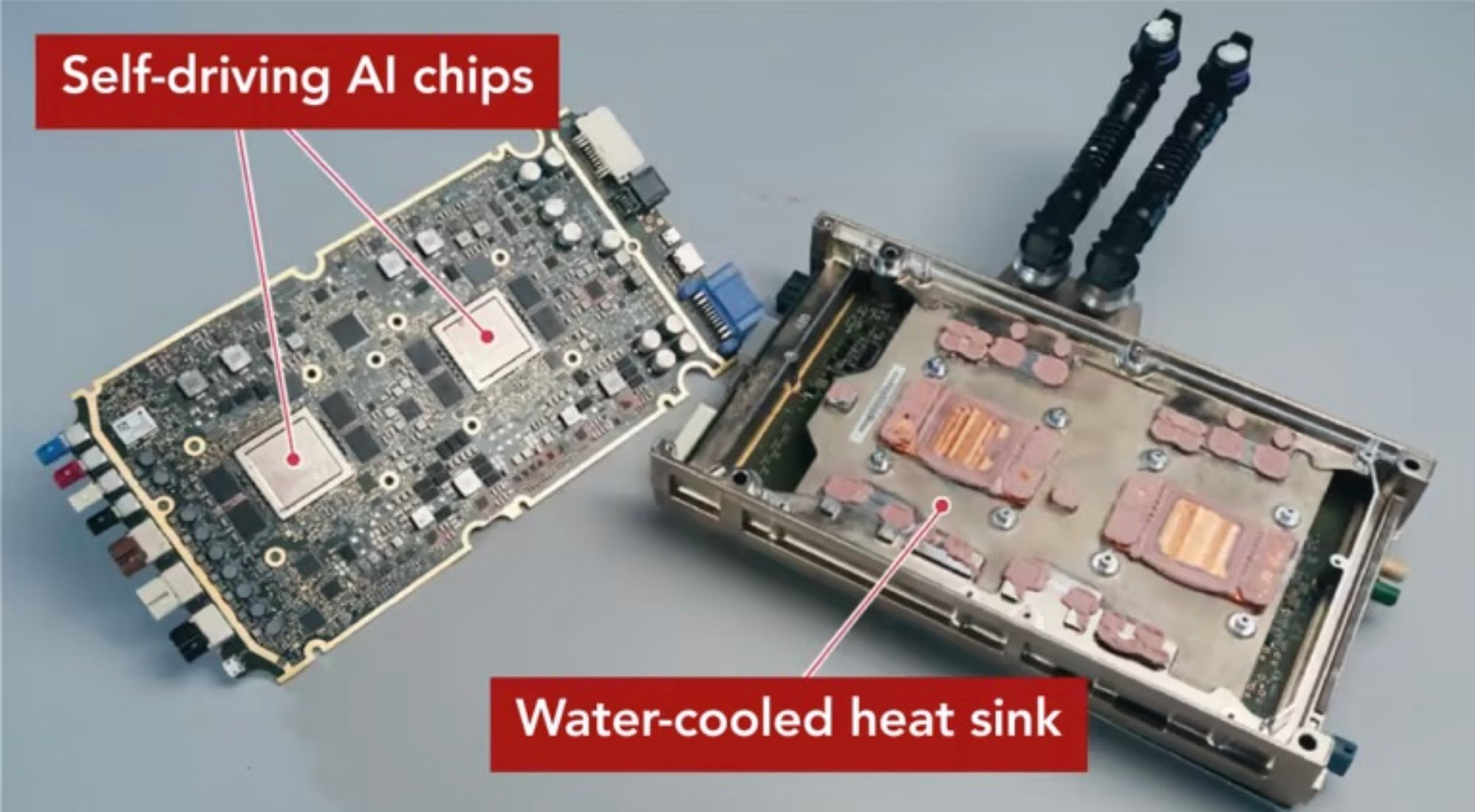
Most parts inside the Model 3 do not bear the name of a supplier. Instead, many have the Tesla logo, including the substrates inside the ECUs. This suggests the company maintains tight control over the development of almost all key technologies in the car.
My takeaway: the relationships big automakers maintain with long-standing supply chains, helmed by whole departments which tend to fight for their own survival, have hindered their progress here.
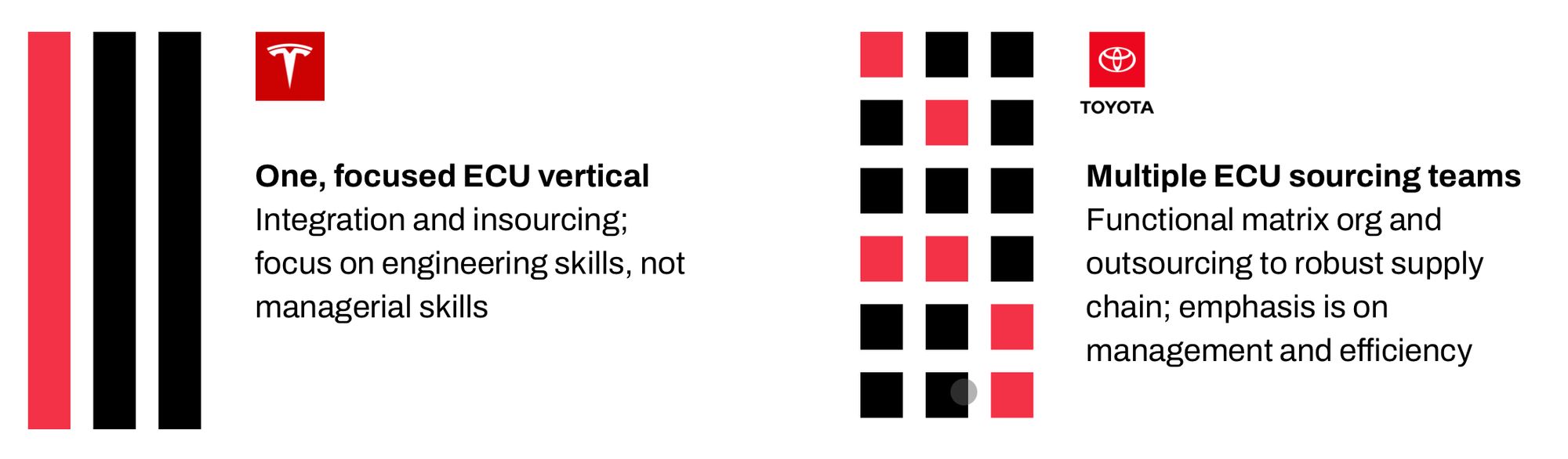
This is a configuration problem. Which organizational “parts,” set up which way, will help the business achieve its strategy? In the case of Tesla vs. Toyota, the parts include external vs. internal suppliers or producers, defined by the goals of the teams associated with that work. Is it “develop the brain for our self-driving future” or “manage the supply chain for XYZ chip-sets”?
Last updated
Was this helpful?